SHOP7D LTD
SHOP7D_1pc 1-12mm CNC 3 Flute Solid Tungsten Carbide Alloy End Mill, DLC Coating, U-Shaped Milling Cutter for Aluminium DAU3E
SHOP7D_1pc 1-12mm CNC 3 Flute Solid Tungsten Carbide Alloy End Mill, DLC Coating, U-Shaped Milling Cutter for Aluminium DAU3E
Couldn't load pickup availability
SPECIFICATIONS
Model Number: DAU3E End Mill for Aluminium
Degree: R0.1
Overall Length: 50mm, 60mm, 75mm, 100mm
Material: Tungsten Cobalt Alloy
Type: End Mill
Diameter: 1mm to 10mm
Coating: DLC
Type1: milling cutter for Aluminium
Material: Tungsten Solid Carbide Alloy
Coating: DLC Coating, more smooth, hight hardness
Hardness: 92HRA
Applicable Material: Aluminium, Copper, wood
CNC or NOT: CNC
Customized or NOT: Can Be Customized
SHOP7D_1pc 1-12mm CNC 3 Flute Solid Tungsten Carbide Alloy End Mill, DLC Coating, U-Shaped Milling Cutter for Aluminium DAU3E
Description:
(1) Type: 3 Flutes Spiral Solid Carbide End mills;
(2) Made of: High-quality Micro Grain Tungsten Steel Solid Carbide;
(3) Shank Diameter: 1mm 1.5mm, 2mm , 2.5mm, 3mm, 4mm, 5mm, 6mm, and etc
(4) Coating: DLC Coating, High Hardness and More Smooth
Best Suitable Materials: Aluminium, Brass,Copper ,other Non-ferrous metals
Applied to:
CNC Router Machining Center, Advertising CNC Router, etc;
Features:
(1) Excellent blades, SHARP cutting edge;
(2) High precision grinded and polished, high abrasion resistance and temperature resistance, good rigidity, not easy to break;
(3) No burrs for staight slot, step shoulder, side face machining;
(4) Specially designed U-shaped chip removal slot, High performance, improve the work efficiency, reduce cost;
DLC coating is a type of carbon-based film coating, with the full name of Diamond-like Carbon. It is formed by depositing carbon ions under vacuum conditions and has high hardness, excellent wear resistance, and low friction coefficient. Therefore, it is widely used in surface treatment of cutting tools in fields such as engineering machinery, automotive parts, and aerospace engines. Hard alloy cutting tools treated with DLC coating can not only improve cutting efficiency and extend service life but also effectively reduce thermal loss and cutting force during cutting, thereby improving product processing quality and stability.
Share
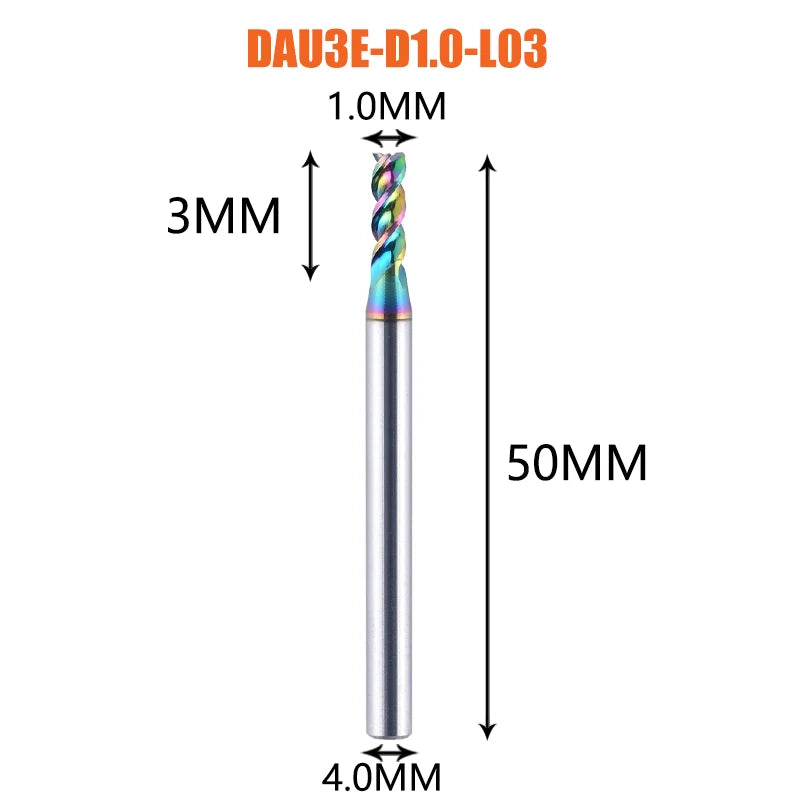


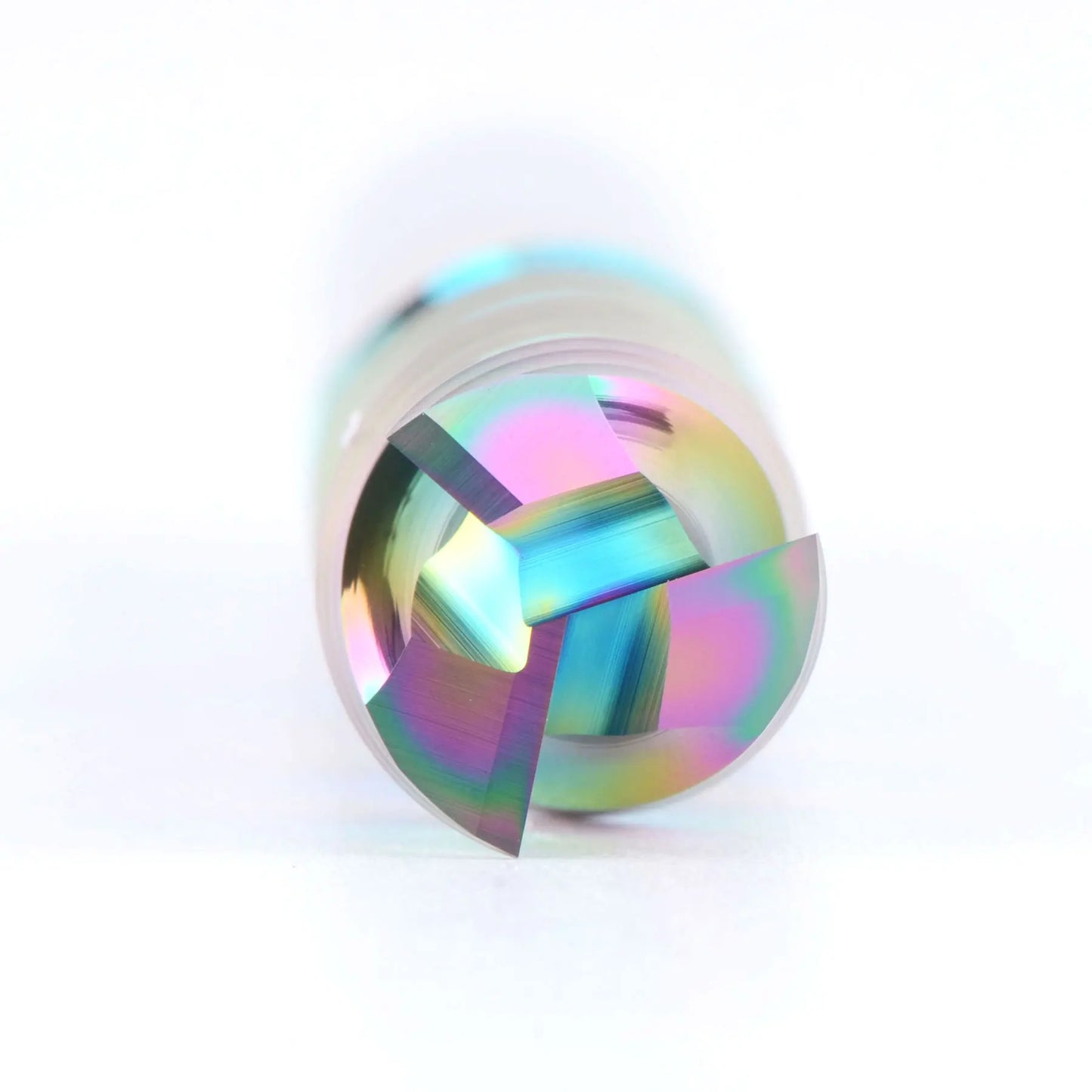
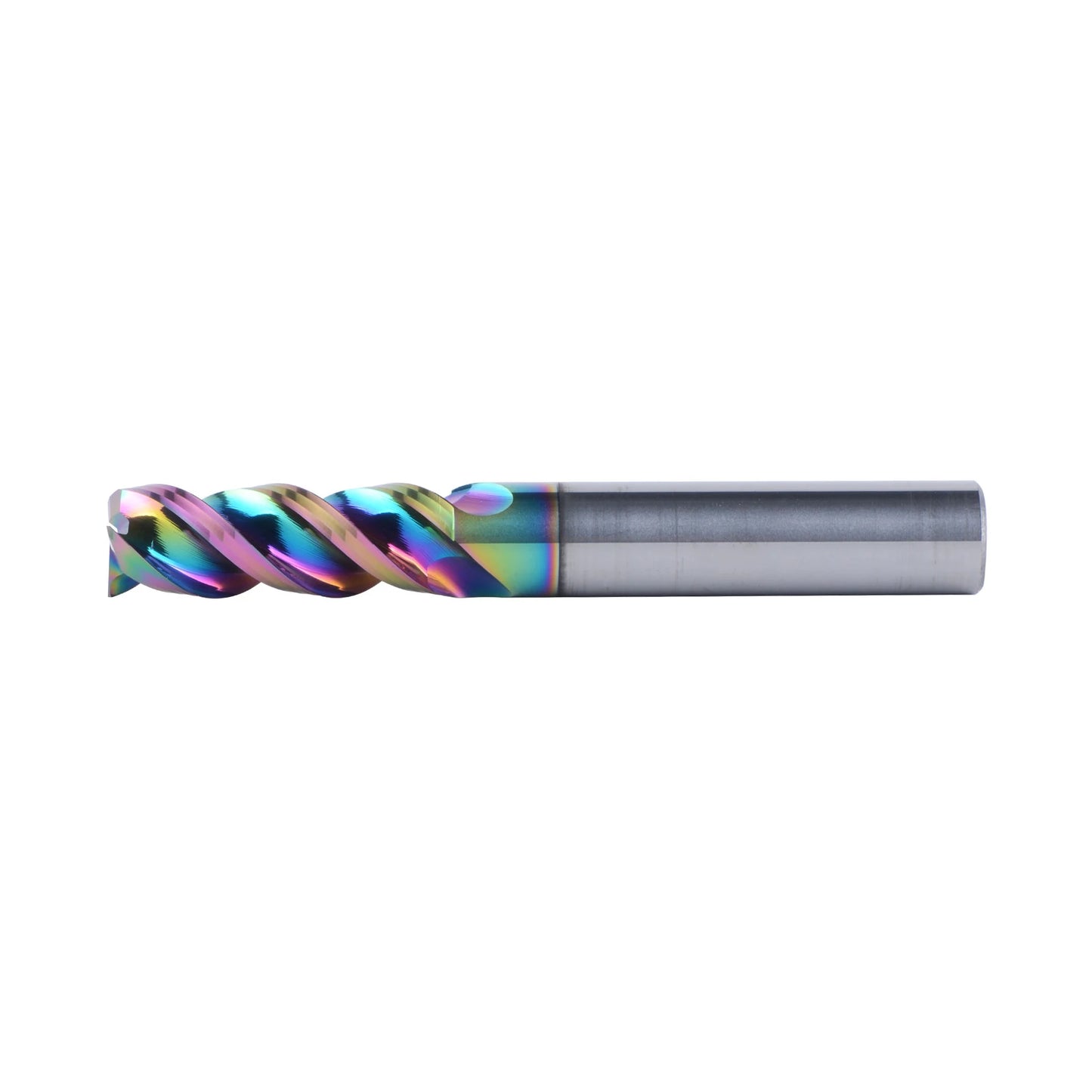
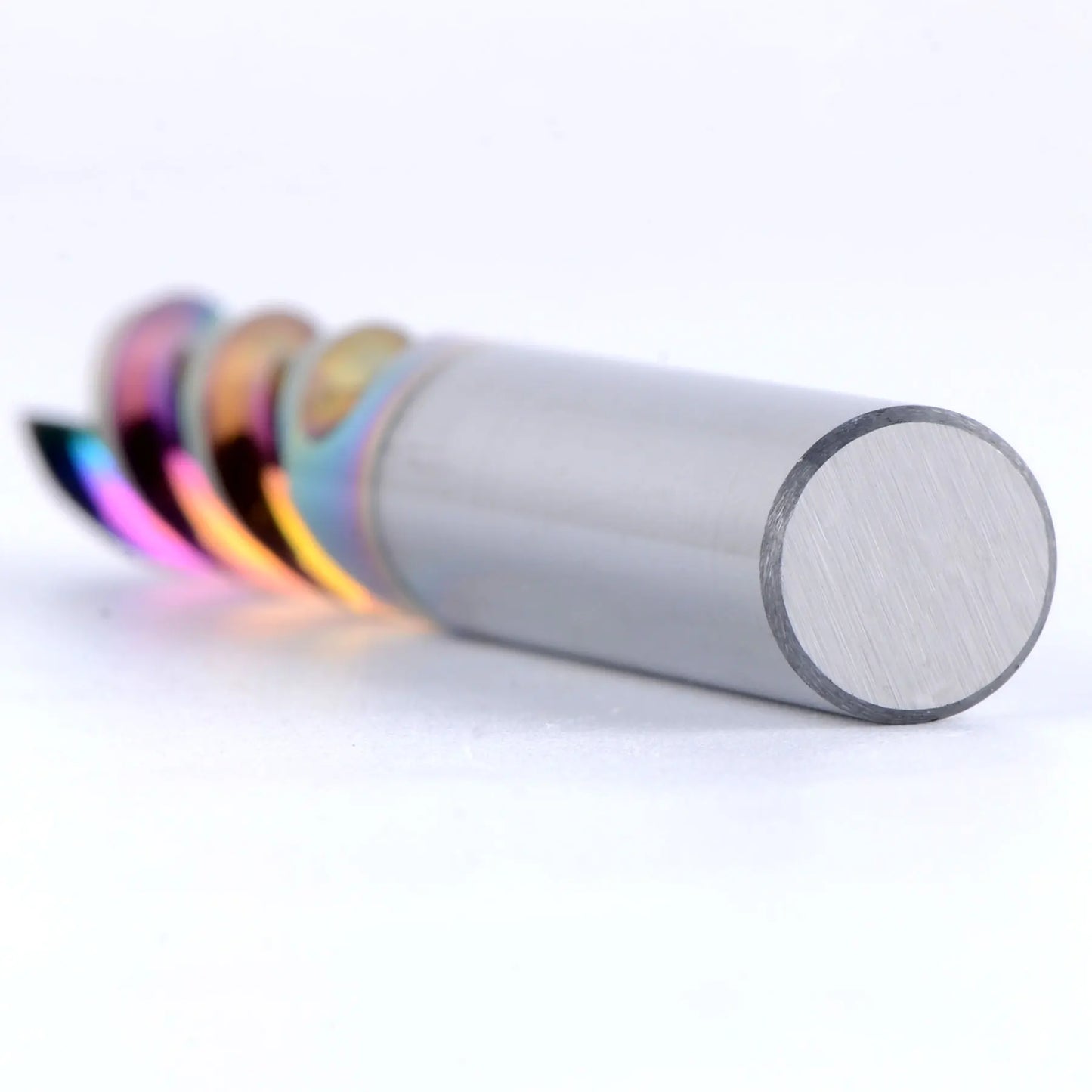
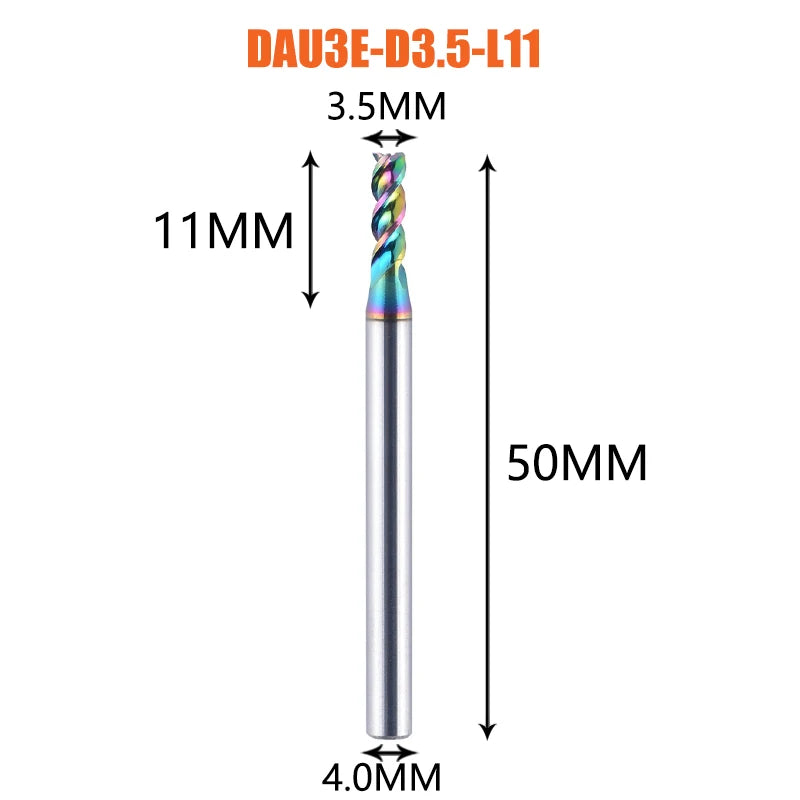
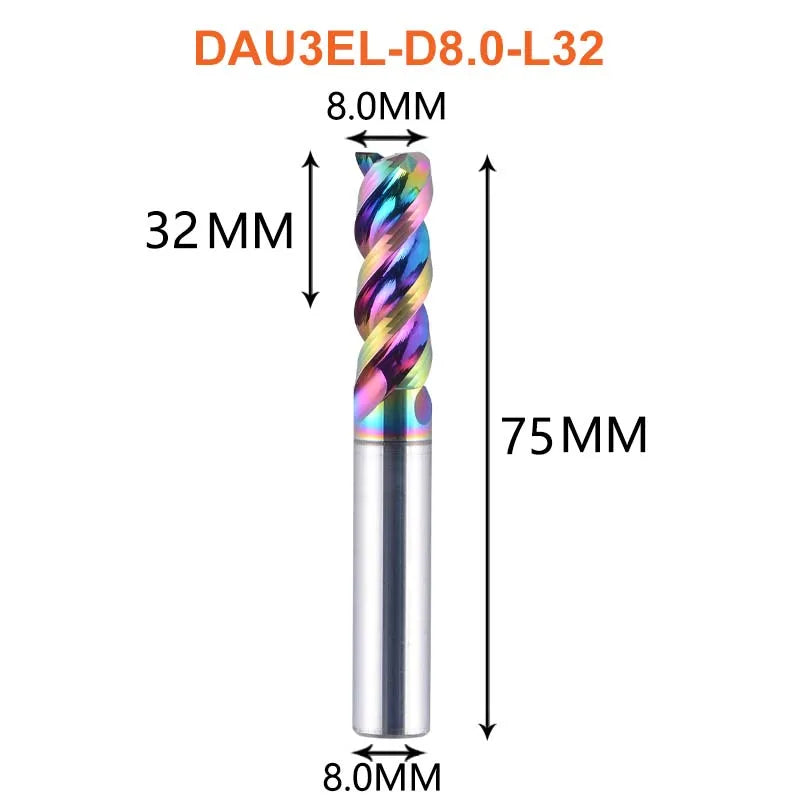
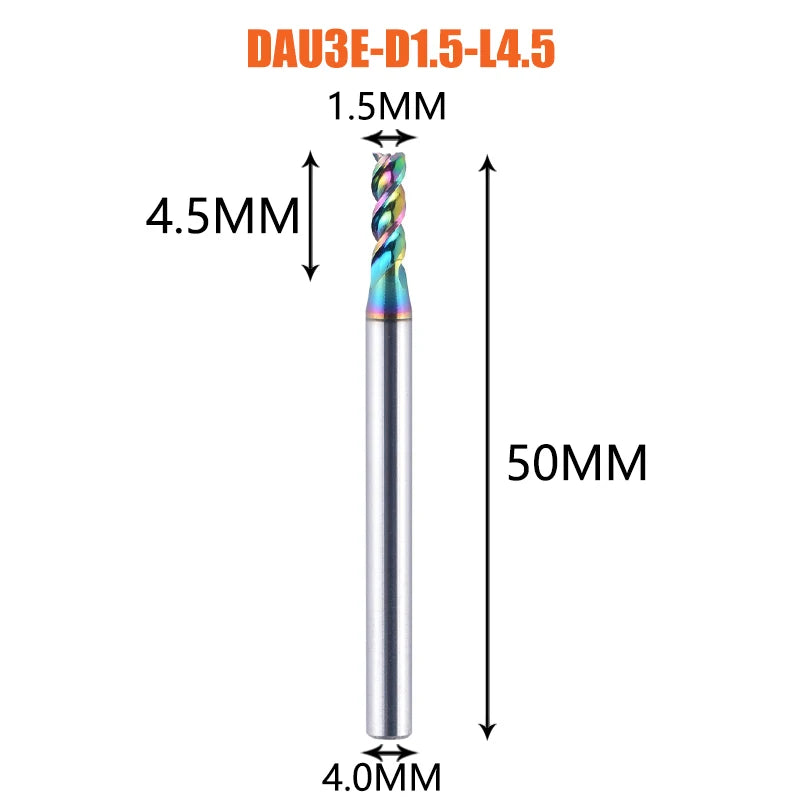
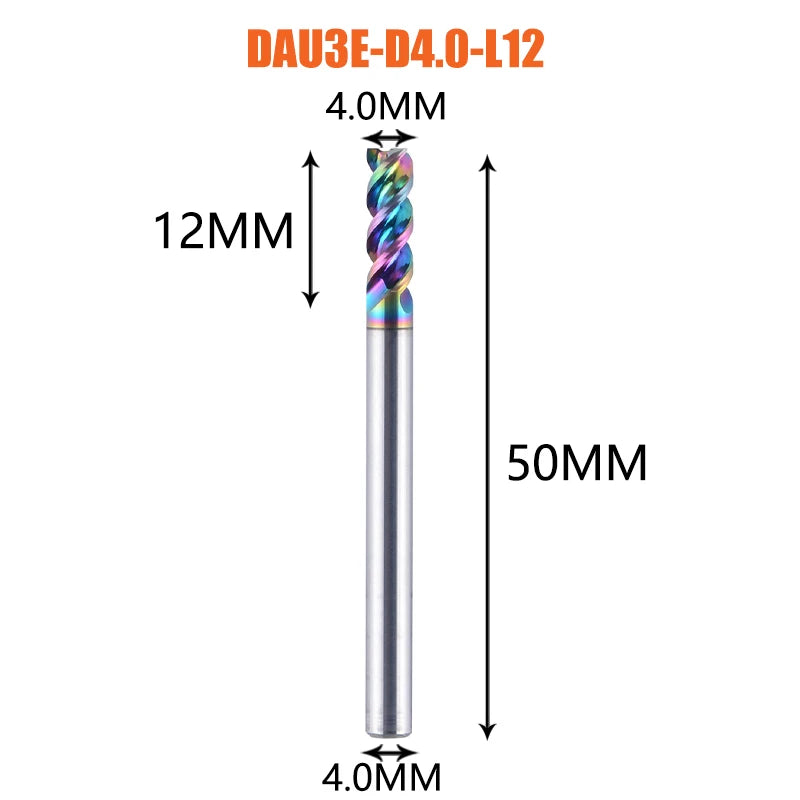
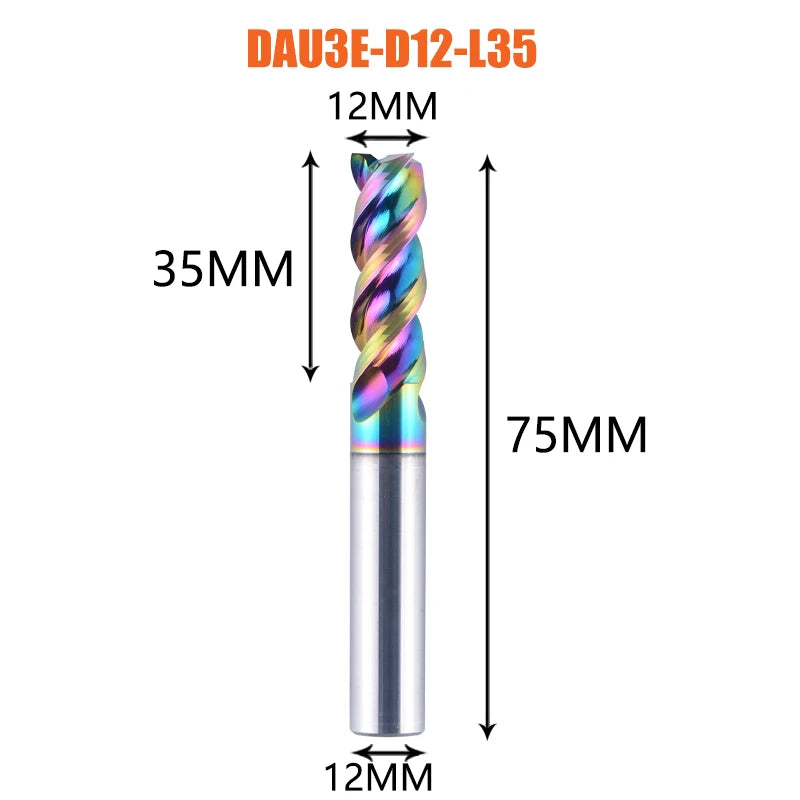

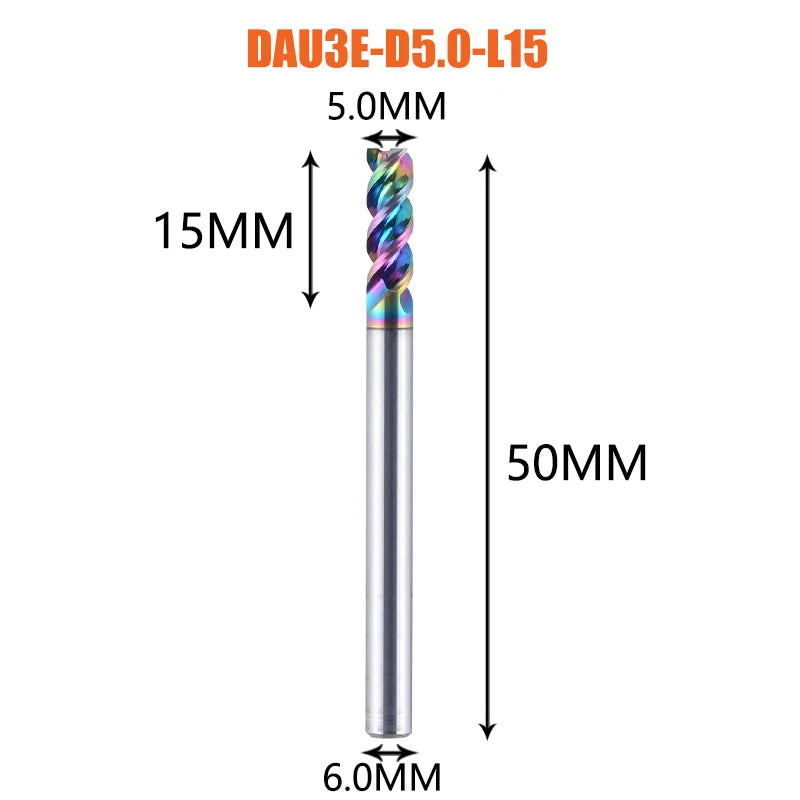
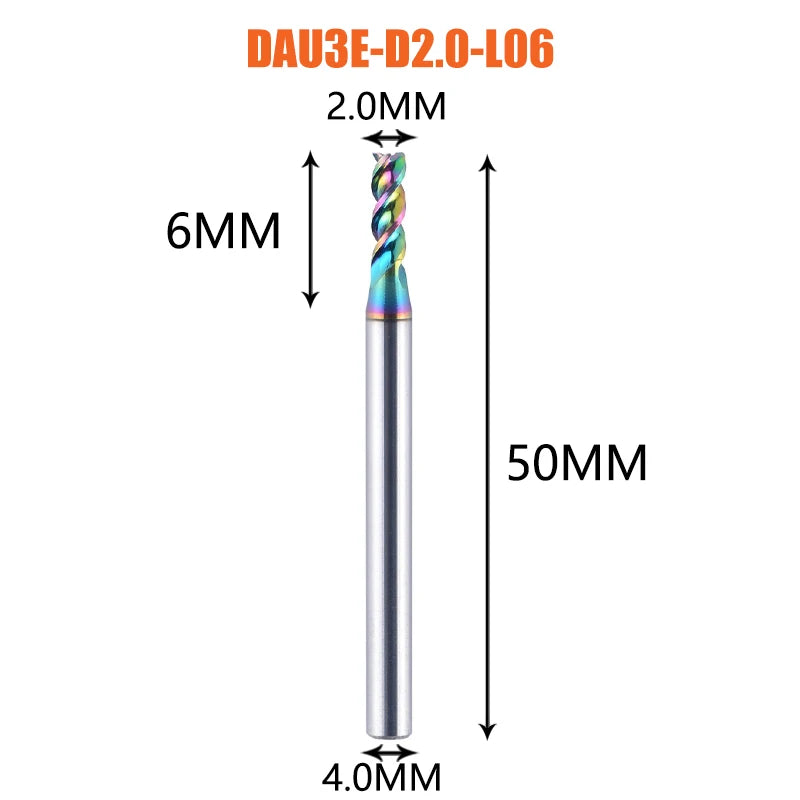
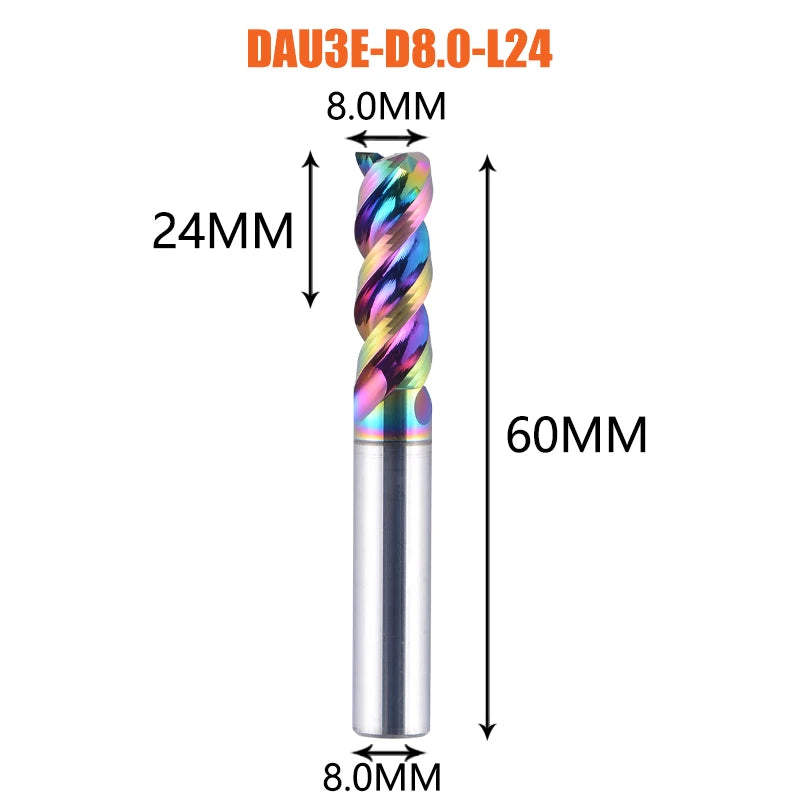
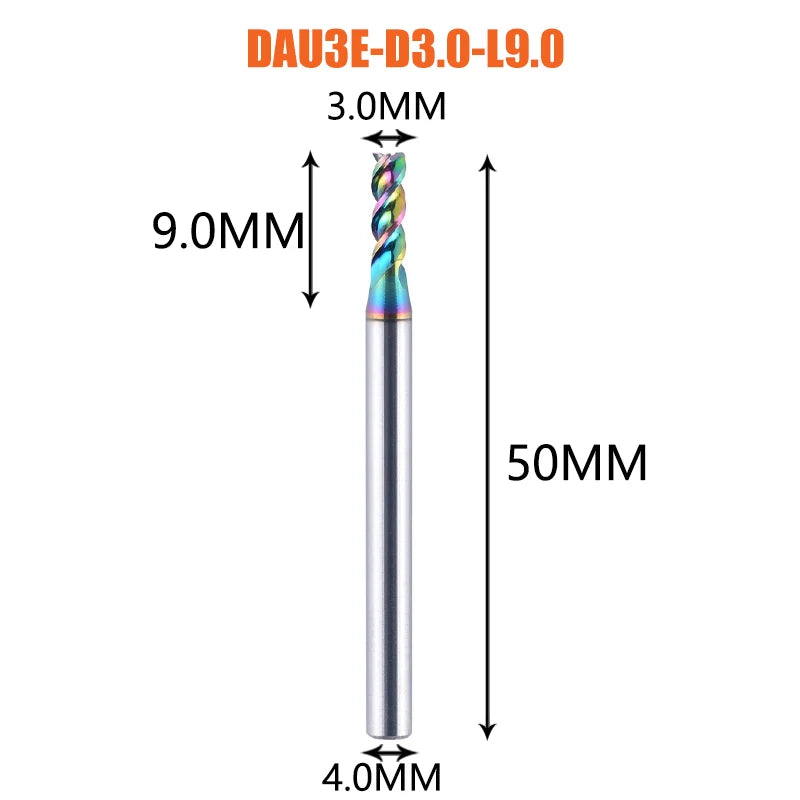
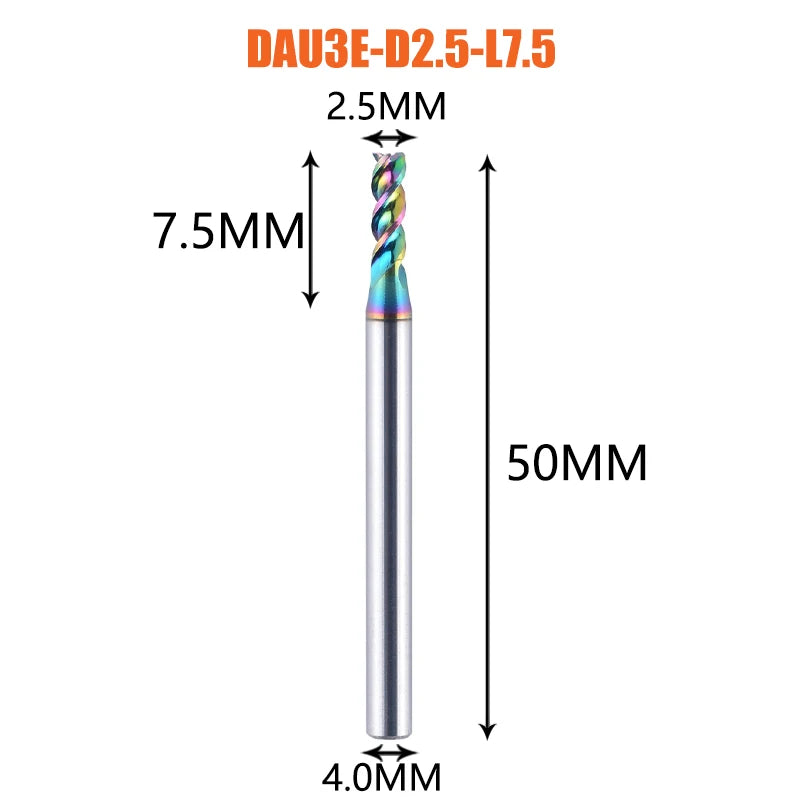
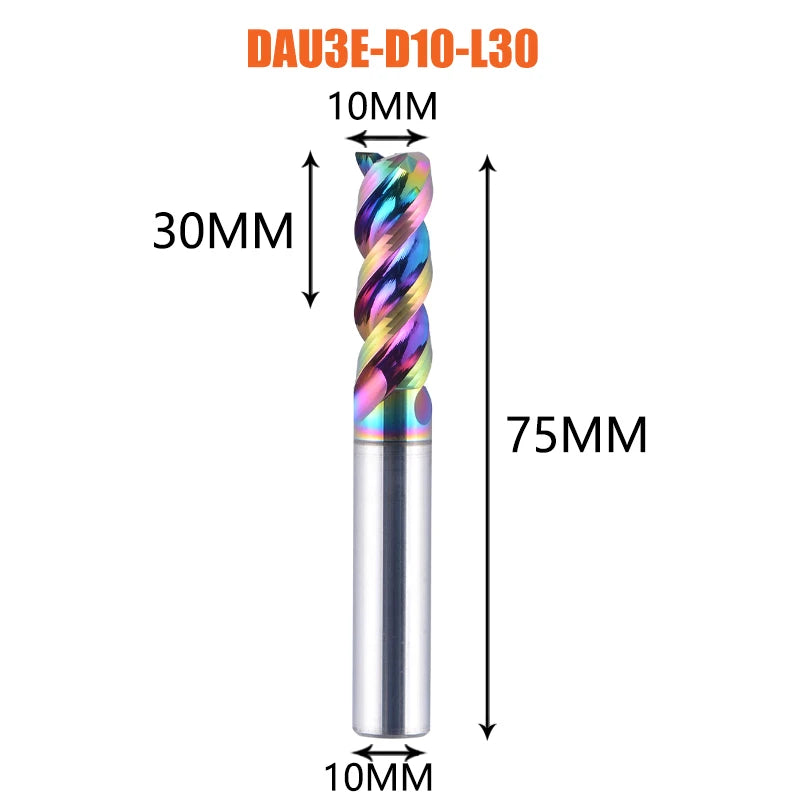